
Material Introduced
Material / Global-Recycled-Standard
Global-Recycled-Standard
The Global Recycled Standard (GRS) is an international, voluntary, full product standard that sets requirements for third-party certification of Recycled Content, chain of custody, social and environmental practices, and chemical restrictions. The goal of the GRS is to increase use of Recycled materials in products and reduce/eliminate the harm caused by its production.

The objectives of the GRS are:
· Track and trace Recycled input materials.
· Provide customers (both brands and consumers) with a tool to make informed decisions.
· Reduce harmful impact of production to people and the environment.
· Provide assurance that materials in the final product are actually Recycled and processed more sustainably.
· Drive innovation in addressing quality issues in the use of Recycled materials.
The Global Recycled Standard is intended for use with any product that contains at least 20% Recycled Material. Each stage of production is required to be certified, beginning at the recycling stage and ending at the last seller in the final business-to-business transaction. Material Collection and Material Concentration sites are subject to self-declaration, document collection, and on-site visits.
Only products with at least 50% Recycled Content qualify for product-specific GRS labeling. See GRS Logo Use and Claims Guide for labeling guidelines.All Recycled materials entering the supply chain shall have a valid Transaction Certificate (TC) issued by an approved CB.
Traders with an annual turnover of less than $10,000 of GRS products, and retailers selling to end consumers only, are exempt from the certification obligation; provided that they do not (re-) pack or (re-) label GRS products. Exempted traders with less than $10,000 annual turnover of GRS products shall register with an approved Certification Body and shall inform the Certification Body immediately once their annual turnover exceeds $10,000, or once they plan to (re-) pack or (re-) label GRS products.


Recycled plastic |
→ |
Sorting washing disinfection |
→ |
Crushing granulation |
→ |
PE particles |
→ |
Recyclable products |
• Recycling of pre-consumer or post consumer materials that have been used in civil, industrial and other purposes and are eventually eliminated or replaced
• Centralized sorting, screening, removal of basic pollutants or bundling of recycled plastics for washing and disinfection
• After pulverization and centralized treatment, the plastic is granulated after drying, dehumidification and other processes
• PE granular material obtained by pelletizing after recycling, used as raw material for industrial production
• Add PE particles made of 20% recycled materials to produce recyclable plastic bags
|

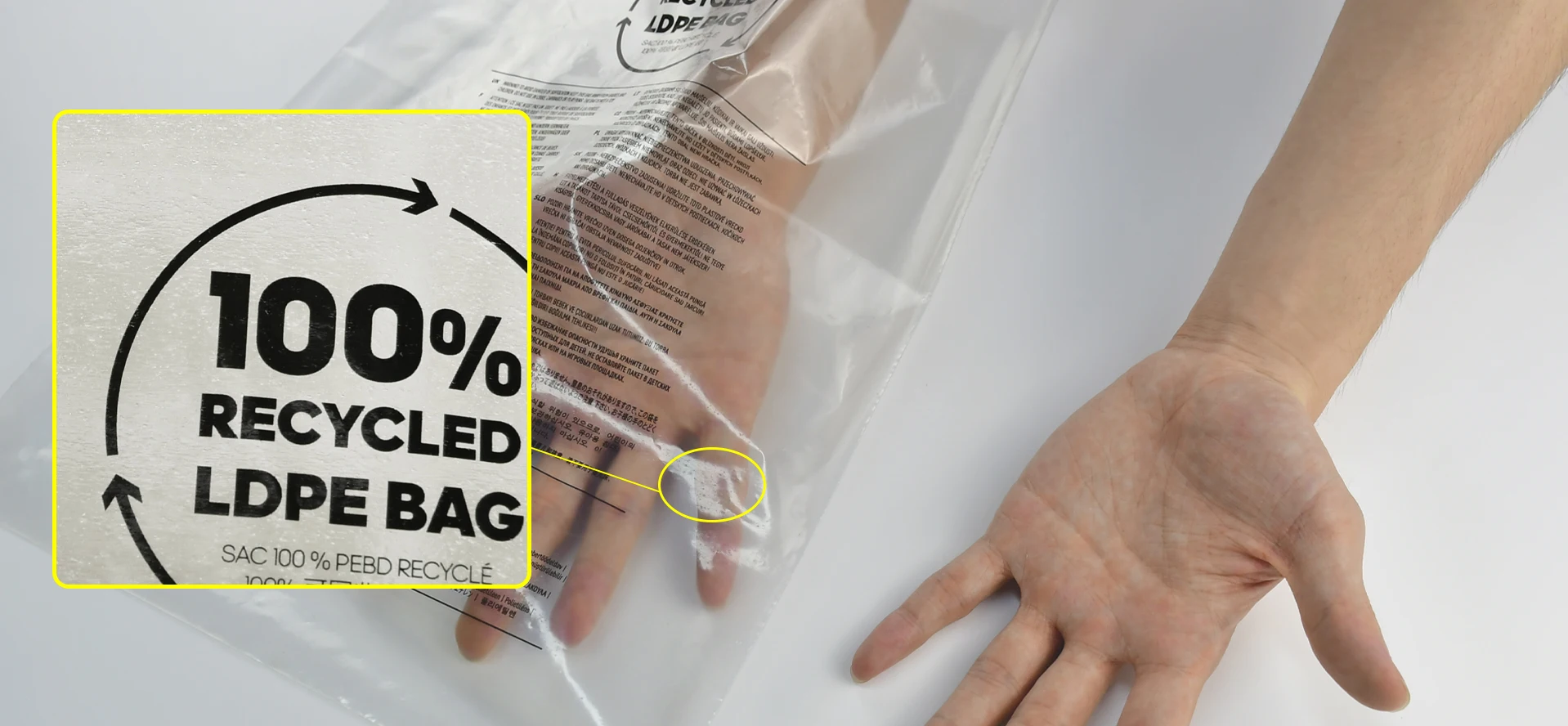
Post-Consumer Material
Material generated by households or by commercial, industrial, and institutional facilities in their role as end-users of the product that can no longer be used for its intended purpose. This includes returns of materials from the distribution chain.
Pre - Consumer Material
Material diverted from the waste stream during the manufacturing process. Excluded is the reutilization of materials such as rework, regrind or scrap generated in a process and capable of being reclaimed within the same process that generated it.
Material / Polylactic acid (PLA)
Polylactic acid (PLA)
The production of polylactic acid is based on lactic acid. Traditional lactic acid fermentation mostly uses starchy raw materials.At present, the United States, France, Japan and other countries have developed and used agricultural and sideline products such as corn, sugar cane, sugar beet, and potatoes as raw materials to ferment lactic acid, and then produce polylactic acid. Corn is the preferred raw material for the biodegradable plastic polylactic acid.
The process of making biodegradable plastic polylactic acid is as follows: first, the corn is ground into powder, the starch is separated, the original glucose is extracted from the starch, and finally the glucose is converted into lactic acid by a fermentation process similar to beer, and then the extracted Lactic acid makes the final polymer, polylactic acid.
Polylactic acid is a biodegradable polymer produced from renewable resources such as grains. In the polylactic acid production route, the lactic acid monomer is first prepared by hydrolyzing grain starch into glucose, and the glucose is converted into sodium lactate by the fermentation process. Lactic acid is further concentrated and then polymerized in the order of polycondensation (to form prepolymer), thermal depolymerization (to form dilactide), ring-opening polymerization, and depolymerization. The molecular weight of the obtained polylactic acid is as high as 75000 g/mol. Lactic acid polycondensation reaction is carried out by conventional methods, and only lactic acid oligomers can be obtained.The most studied method for preparing high molecular weight PLA is through the ring-opening polymerization of lactide, which is synthesized from lactic acid oligomers through high-temperature cracking.
There are detailed reports on the mechanism and reaction conditions of the ring-opening polymerization of lactide. Japan's Mitsui Chemicals Co., Ltd. proposed a new technology to prepare polylactic acid directly by lactic acid polycondensation reaction without lactide. This technology uses a highly active catalyst to obtain high molecular weight polylactic acid through solution polycondensation.
Polylactic acid (PLA):
Because lactic acid and lactide contain asymmetric carbon atoms, PLA with different stereoregularities, such as L-PLA, D-PLA and DL-PLA, can be obtained by polymerization. The degradation of PLA is divided into two stages:
1) First, it is pure chemical hydrolysis to lactic acid monomer;
2) The lactic acid monomer is degraded into carbon dioxide and water under the action of microorganisms. The food cup made of polylactic acid can be completely degraded in only 60 days, which truly achieves the dual effect of ecology and economy.
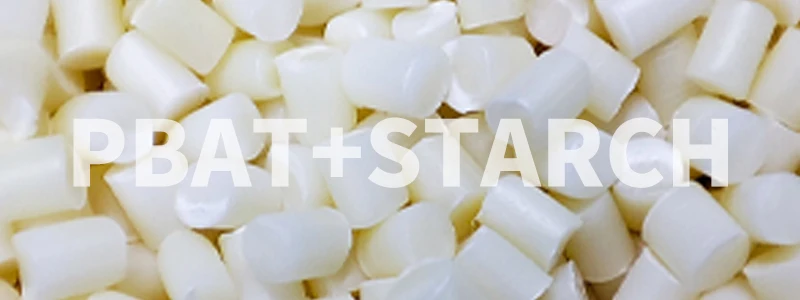
PBAT (polyterephthalic acid/adipic acid/butanediol):
Itself is a biodegradable material, it is a material with lower cost, high mechanical properties, good biosafety, and PBAT production with independent intellectual property rights Process and complete sets of production and application of patented technology. PBAT is also a polymer material, which can replace ordinary disposable plastic bags in use.
There are 5 different combinations of raw materials for fully biodegradable plastic products, PBAT+PLA (polylactic acid) or starch plastic is a cost-effective combination.
Plant |
→ |
Corn starch |
→ |
PLA+PBAT |
→ |
Product |
→ |
Organic soil |
• Plant - Organic fertilizer can be used for crop growth
• Corn starch - With corn flour/cassava/grain starch,etc
• PLA+PBAT - Out-and-out biodegradable
• Product - Corn starch biodegradable producus
• Organic soil - Garbage can turn into organic fertilizer
|
Material / Ecopure
Ecopure
Since its inception, plastics have been widely used in various fields of the national economy, such as the packaging industry and the disposable product industry, bringing great convenience to human production and life. However, The world already produces more than 8 billion tons of plastic,its huge use and waste have led to increasingly serious environmental pollution - "white" pollution, including river pollution, farmland mulch pollution and marine plastic pollution. 9% of it is recycled and 90% is landfilled, incinerated and thrown into the sea. As we all know, burning plastics will cause air pollution and environmental damage. Traditional plastics need to be degraded in 500-800 years by landfilling, which will waste the world's land resources.
ECOs are a class of plastics that degrade due to the action of naturally occurring microorganisms such as bacteria, molds (fungi) and algae.
Features of ECO material:
1 Specially developed for biodegradation in anaerobic landfills, it can be biodegraded in landfills. After adding ECO, plastics can be biodegraded in landfills through anaerobic digestion, and can be naturally decomposed in household composting.Tested according to ASTM D5511
2 Clean and renewable energy: only water, carbon dioxide, bath gas and biomass (humus) are produced during the decomposition process. Tested according to ASTM D5511
3 Clean and Safe: Biodegradation in 1-5 years, no residue after biodegradation, just like organic matter, microorganisms will continue to eat ECO treated plastic until nothing is consumed, the rest of the materials are natural. Tested and passed ASTM E1963 BDP simply enhances natural processes by allowing microorganisms to enter the polymer chain
4 There will be no change to the original physical properties of the plastic, no need to update the production machinery and equipment, the product can be recycled and reused without landfill, and the use time is long
How does ECO work?
Oil is converted into hydrocarbons by microorganisms from organic decay below the surface, and the remaining organic matter buried in the deep underground undergoes decomposition and complex chemical reactions under temperature and other factor to generate oil.
We process petroleum products into various plastic products, and ECO-plasticizer attracts anaerobic bacteria and anaerobic organisms to biochemically reduce plastic products to the original state before the formation of petroleum — organic corrosives, forming a closed loop.

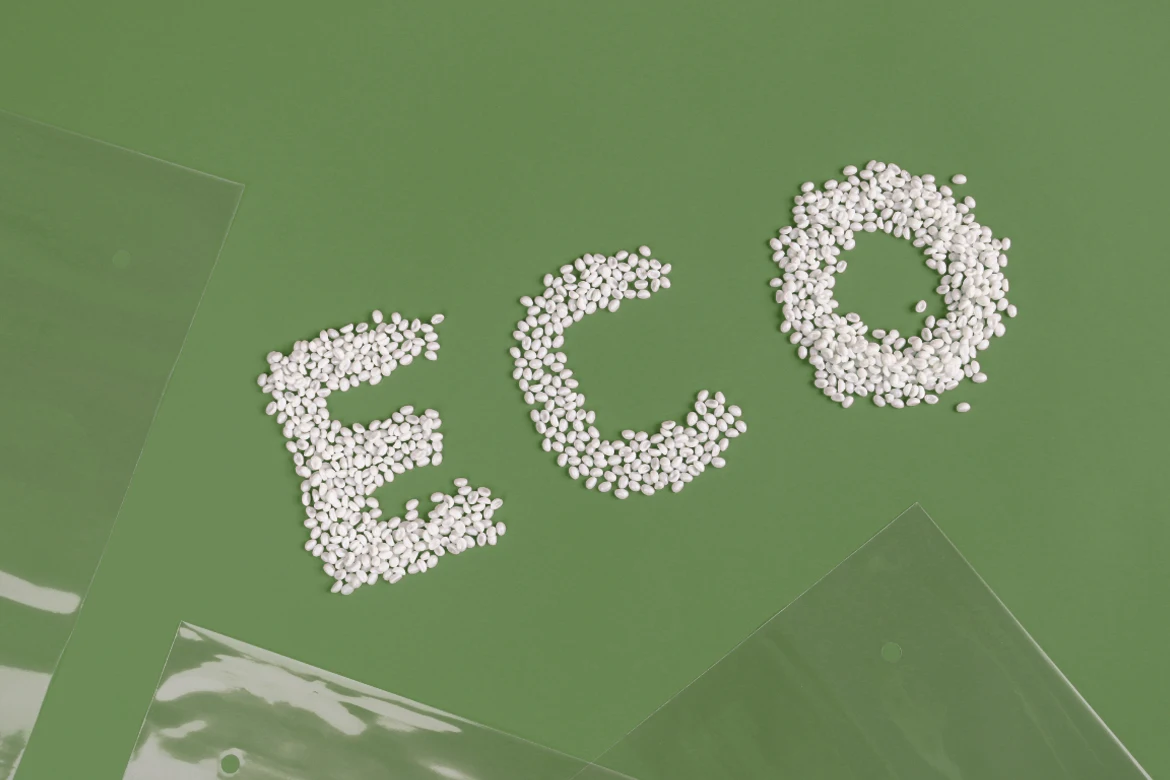
What is ECO?
ECO is an organic additive used to accelerate plastic, rubber and PS foam products in landfills (landfills and deep seas) full of active anaerobic organisms
The process of making the plastic biodegradable is mixed with the existing plastic material, and then directly blended into the extruder through the hopper. It can also be added and used in proportion online together with a quantitative weighing system.
According to different types of plastics and different models, they are all added at a rate of 1%.
Application: Any polymer type such as PVC, PET, PP, PO, PE, PC, PS, etc.
Compliant with FDA/EU/GB standards and safe with REACH, ISO, ROHS, EFSA, EINECS, CFIA, and can be recycled many times.
ECO products are made from traditional plastics injected with anaerobic organic additives, which introduce plastics into the biodegradation stage through chemical activity caused by bacteria, leaving only natural gas and bioenergy at the end.
Material / D2W
D2W™
d2w™ grade 93389/C is an oxo-biodegradable additive based on a polyethylene carrier resin formulated for demanding processing application requiring a high degree of thermal stability, D2W appears as light brown particles.The product should be stored in cool dry conditions away from strong sources of light and heat. Storage temperatures should not exceed 30°C.
Under normal storage conditions the product has a shelf life of 18 months from the date of manufacture which is printed on the sack.Part used bags should be discarded.
D2W is an additive formulation that renders conventional polyolefins oxo-biodegradable.“Oxo-biodegradation” is “degradation identified as resulting from oxidative and cell-mediated phenomena, either simultaneously or successively” ("Terminology in the field of degradable and biodegradable Polymers and Plastics" CEN/TR 15351).
Polyolefin products made with d 2 w additive will abiotically degrade in the presence of oxygen. Degradation has been proved in accordance with the requirements of ASTM 6954-04 by passing ASTM 5510(RAPRA Report 46095).
The ability of d 2 w products to comply with the biotic (biodegradation) tests of ASTM 6954-04 has been demonstrated by the loss of molecular mass achieved after abiotic thermal degradation, resulting in ultimate biodegradation of the material into CO2, water, mineral salts and biomass (RAPRA Report 46303, Pyxis report 30.7.05, and DPPA Chapt. 3, Eco-sigma Report Sept. 2008).
The eco-toxicity sections of EN 13432 and ASTM 6954-04 require that no harmful residues are left - this has been verified for d2w additive. (OWS Report MST-4/1-d2wb&d2wc, Eco-Sigma Report Sept.2008).D2W additive does not contain heavy metals (defined by 94/62/EC Art 11 as lead, mercury, cadmium, or hexavalent chromium).
d 2 w additive is safe for direct food-contact according to the European Union requirements for Direct Food Contact 1935/2004/EC and the US FFDC Act and regulations (RAPRA report 46137, and Keller &Heckman certificate 18.2.2009). It is the responsibility of the manufacturers of products intended for food-contact to ensure that all other materials incorporated by them comply with those requirements.
If polymer products are correctly made with d 2 w, the additive will have no effect upon the strength and other performance characteristics of the product during its programmed service-life.Polymer products correctly made with d 2 w comply with the Essential Requirements of the EU Packaging Waste Directive 94/62/EC Annex II paras. 1, 2 and 3(a) (b) and (d).In addition to the above, d 2 w Additives and finished products have been extensively tested, according to the test methods prescribed in the UAE Standard 5009/2009 and BS8472.d 2 w products can met AFNOR TC51-808 Accord.
D2W packaging film degradation stage diagram |
1 Month
The packaging film in this picture has been added with D2W oxidized biodegradable plastic additives and is set to decompose after 18 months
18 Months
The packaging film after the 18th month had cracked. Because D2W oxidative biodegradable plastic additives contain natural mineral salts and degrading substances, they can promote the weakening and decomposition of polymer plastic chains
19 Months
The packaging film in the 19th month has been completely broken
20 Months
The packaging film of the 20th month, small fragments whose molecular weight has dropped below 40,000. At this time, microbial biomass in the normal natural environment can erode these biological medium fragments. In the end, all that's left is carbon dioxide, water, cellular biomass, and nothing harmful remains.
D2W oxo-biodegradable plastics are not currently intended for composting.If sent to landfill d 2 w oxo-biodegradable plastics will degrade in aerobic conditions. In anaerobic conditions they become inert and will not emit methane.d 2 w oxo-biodegradable plastics can be recycled together with ordinary oil-based plastics. For long-life products, stabilisers should be added if necessary.
Symphony’s d2w® technology is the only oxo-biodegradable plastic additive certified by ABNT under the Environmental Quality–Eco-Label program Internationally accredited by INMETRO – Certificate no 365.001/14